Four Ways to Revamp IT Rollout Efficiency for Retail
The process of rolling out new technology into your stores. It’s a flawless and simple joy, right? It starts as a clear and easy plan on a spreadsheet but ends up a messy series of poorly timed shipments and badly configured devices, leading to a lot of emails creating inefficiency and frustration. Ever found yourself marveling at how your best laid plans are dashed against reality? Or how your implementation partners vanish into thin air during deployments? Or perhaps you’ve witnessed the “budget bloat” that happens when inefficiency in your rollout creates delays and re-work that are blamed on ‘supply chain issues’. Fear not, weary retailers, there exists a better way to manage this process.
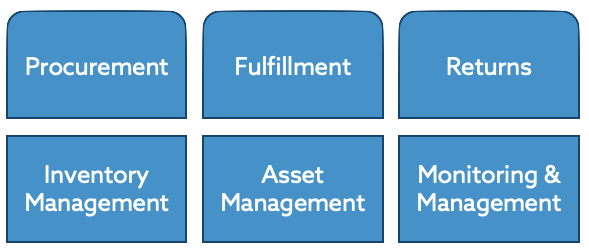
Bringing Order to the Chaos
Retailers, in their steadfast effort to modernize, encounter a formidable challenge. Implementing new technology across numerous stores is comparable to managing a complex array of IT equipment, each with unique configuration requirements. The hurdles are abundant, much like the frequent issues with point-of-sale systems or wifi. These include discrepancies in deployment times, lost shipments, and the perennial “it worked fine in testing” dilemma.
We believe that an integrated approach that links inventory management, asset management, remote management & monitoring and shipping logistics, into a single platform is the only way to maximize the efficient management of IT assets in a dispersed environment like retail.
This enables retailers to pull four important factors into control in the management of their IT rollouts:
1. Track Procurement and Warehousing
Before any rollout begins, it’s crucial to efficiently catalog and organize all your devices. You may be doing this in a spreadsheet or maybe an asset manager, but you need to manage the workflow also. Even a small rollout can become overwhelming without proper organization, and many devices need to be ordered in advance to ensure availability when needed. Without systematic tracking, finding everything during the shipping phase can be time-consuming.
Montra’s device lifecycle platform, Via, addresses these challenges effortlessly. Designed specifically for IT, Via enables seamless tracking from procurement to deployment. It keeps tabs on software revisions, warranty dates, and service ticket history. By integrating with your ordering and shipping processes, Via simplifies procurement and warehousing complexities, ensuring every device is accounted for and ready for use.
For warehousing, Via allows you to track devices down to the pallet or individual shelf location. You can even track devices by serial number and manage IT asset details like software versions and hardware warranties. The platform also supports creating bundles and setting kitting requirements for interdependent devices. Any rollout process can be initiated within Via or through service management platforms like Salesforce Service or ServiceNow.
2. Monitor Shipping Centrally
Once devices are ready to go, the shipping process often turns into a disorganized mess of tracking numbers across multiple carriers. Whether you are shipping a bundle of devices to a single store, or a fleet of devices across multiple stores, using spreadsheets to track all your shipments can quickly get out of control.
With Via you can initiate and track all shipments from one location. You can ship bundles of devices with the same ease as a single unit. You can also specify requirements for pre-configuration or kitting prior to shipment, and you can even indicate whether an installer is needed on site to meet the devices.
Once devices are shipped, they can be tracked directly in Via with real-time updates from UPS or FedEx fed directly into the system – even across multiple accounts numbers. No more tracking packages across multiple carriers and various carrier accounts.
3. Monitor Devices in the Stores
Ensuring ongoing performance and swiftly addressing failures are critical aspects of IT efficiency in retail. Once devices are deployed, they should be continuously monitored for security and availability. Real-time surveillance allows for the immediate detection of security issues or system failures, ensuring that any problems can be addressed before they escalate.
Via integrates device monitoring with logistics and asset management to greatly improves response efficiency. Knowing the origin, duration, imaging history, and spare inventory of each device throughout its lifecycle streamlines issue resolution.
This integrated approach not only reduces resolution and response times but also minimizes downtime and employee time spent on technology issues rather than customer service. This leads to an enhanced customer experience, increasing sales and promoting repeat visits. A single, system of record for devices, like Via, also eliminates the need to maintain multiple databases of devices for warehousing, for device monitoring and for asset management.
4. Manage Returns and Spares
Furthermore, when it comes to the inevitable hiccups that require a system to be returned or replaced, Montra Via also streamlines this process. The platform’s efficient returns processing mechanism simplifies the logistics of initiating the return of a failed device and ordering a replacement from the spares inventory with minimal disruption. Designed for standard returns or cross-shipped ones, Via reduces downtime, ensuring stores quickly receive the correct equipment with an accurate configuration. By making returns processing seamless, Montra Via protects retailers from the potential chaos caused by device malfunctions, thus maintaining high operational standards and customer satisfaction.
Montra Via also helps you manage your spares inventory with a separate inventory account for spares systems and parts. Importantly you can see set reorder alerts, see versions and updates, as well as warranty dates. This help makes certain that your spares are up to date and ready if a return is required.
As retail continues to get more tech-enabled, implementing Montra Via for your IT logistics is akin to upgrading from a cash register to a modern POS system. Cost efficiency, faster deployment, better uptime, streamlined cybersecurity, efficient inventory management, and improved spare device storage aren’t just aspirations; they are your new reality.
Retailers, elevate your tech rollout game now. Life is too short for inefficient IT deployments. Join those who refuse to accept the status quo, empowered by the revolutionary capabilities of Montra Via. Your future self—and your bottom line—will thank you.